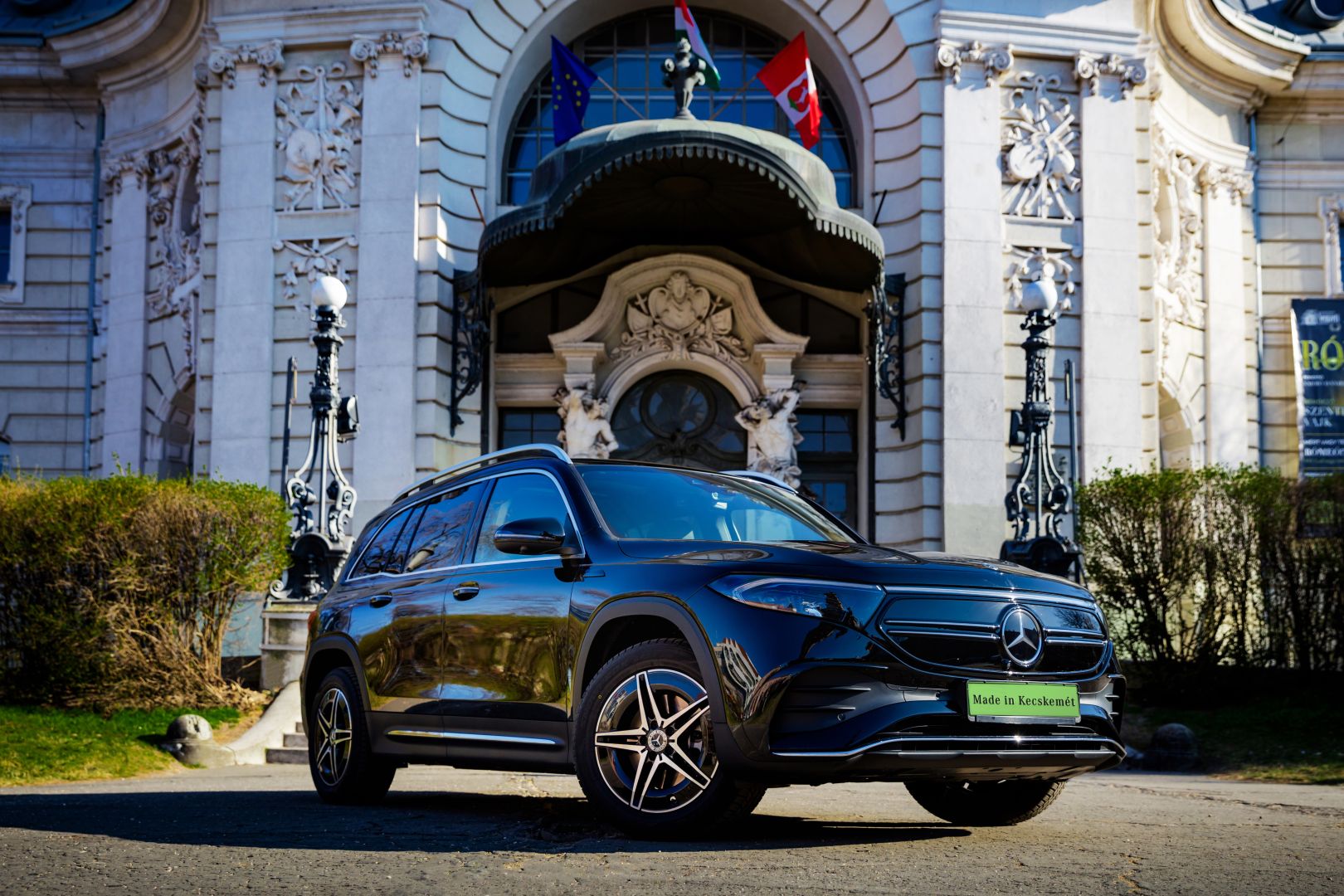
As a result of its diverse and complex corporate social responsibility the plant provides support to educational and cultural organizations, foundations, and various institutions.
The plant attaches great importance to supporting community events that offer quality recreation in the city and in the region.
The plant is committed to conventional social and charitable purpose activities. Tasks considered important by the plant include improving the quality of life for people with disabilities, and supporting disadvantaged children and their families as well as organizations that represent them. The plant participates in charitable initiatives several times a year, supports the city hospital’s work, and provides financial assistance for the operation of public benefit foundations.
The plant involves employees in the implementation of its social responsibility goals by carrying out activities of smaller or larger scale: tree planting, waste collection, fundraising, renovation programs. Sustainability is a key area of the plant’s corporate policy and strategy, so the plant places special emphasis on complying with it in its daily processes.